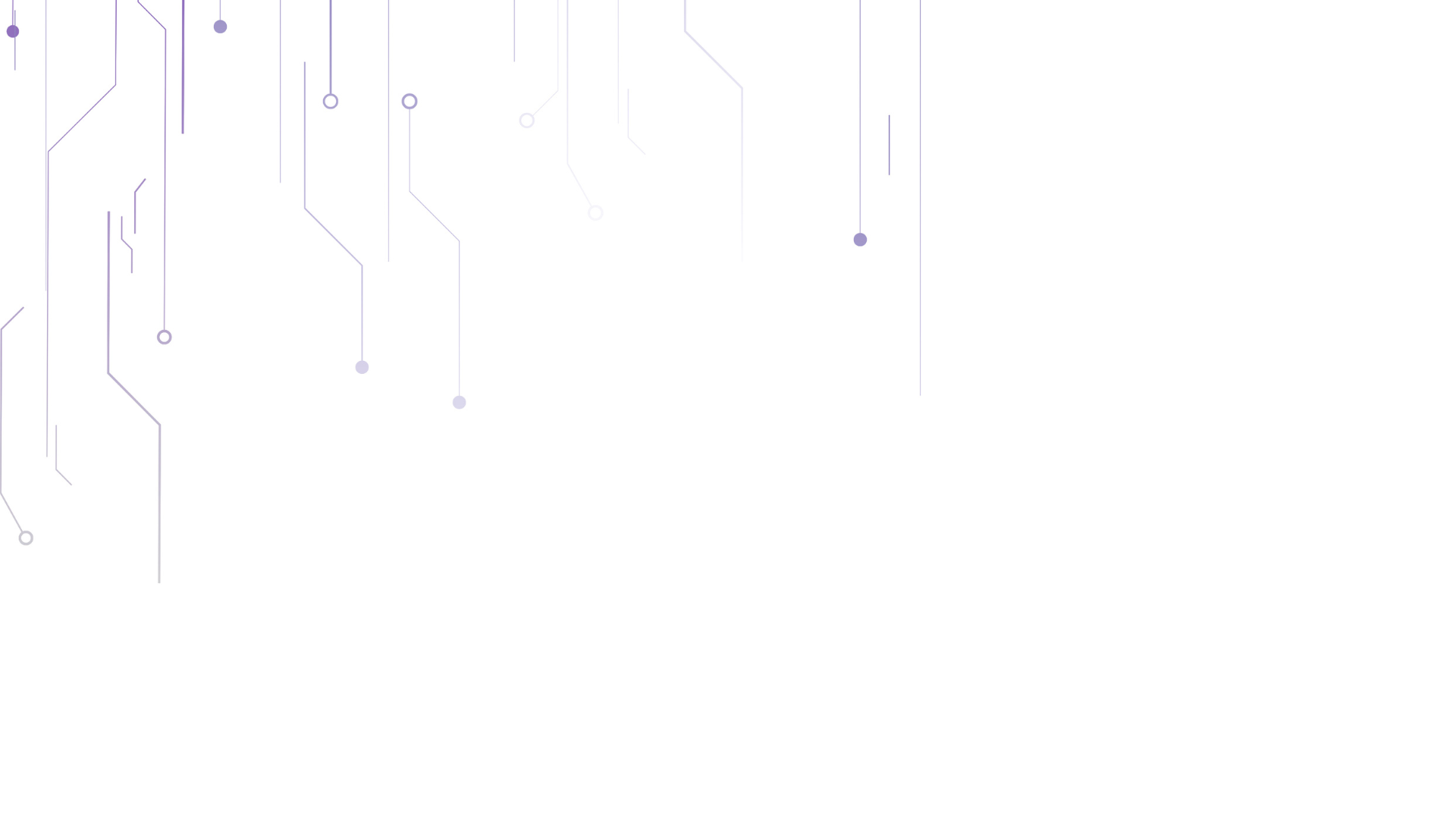
6 Proven Inventory Optimization Techniques for the Aviation Sector
Discover the art of precision in aviation inventory management. From data-driven demand forecasting to JIT strategies, safety stock, and tracking technology, we unveil the steps that keep planes in the sky and operations seamless.
Waqar Jadoon - CEO Vantage Plus
8/25/20232 min read
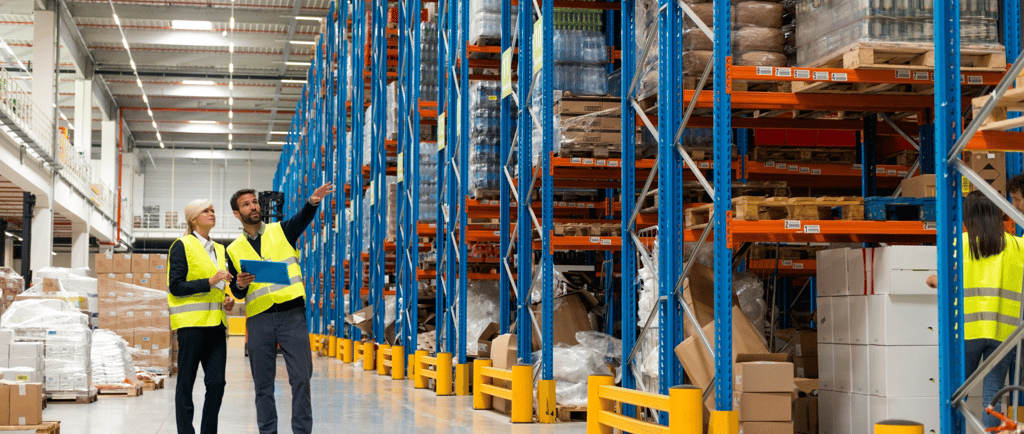
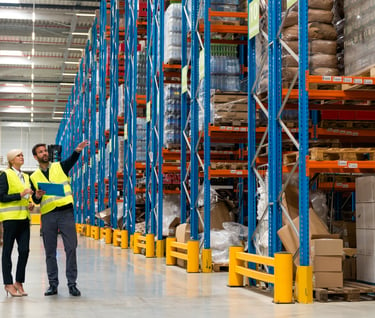
Optimizing Inventory Management: Key Steps for Aviation Supply Chains
Introduction
In the fast-paced world of aviation, where every second counts and precision is paramount, efficient inventory management is the unsung hero that keeps the industry soaring. Striking the delicate balance between having enough spare parts to ensure smooth operations and minimizing excess inventory to cut costs is a complex dance. In this blog, we will unravel the key steps to optimize inventory management for aviation supply chains, ensuring that planes stay in the sky and operations remain seamless.
Data-Driven Demand Forecasting: Navigating Future Needs
Imagine having a crystal ball that reveals the future demand for spare parts. While we can't quite conjure magical spheres, data-driven demand forecasting comes close. By analyzing historical data, flight schedules, maintenance trends, and market dynamics, aviation supply chains can accurately predict which parts will be needed, when, and in what quantities. This foresight empowers supply chain managers to stock the right parts at the right time, minimizing costly shortages and surplus.
ABC Analysis: Sorting Priorities
Not all spare parts are created equal. Some are crucial for keeping flights on schedule, while others can afford to linger in storage. ABC analysis categorizes parts into three groups: A, B, and C, based on their importance and value. Group A comprises high-priority items, B includes moderately important ones, and C encompasses low-value parts. By stratifying inventory in this manner, supply chain managers can focus efforts and resources where they matter most.
Just-in-Time (JIT) Inventory: Precision at Its Best
In the world of aviation, every inch of space is precious. Just-in-Time (JIT) inventory management ensures that spare parts arrive precisely when they're needed, eliminating the need for extensive warehousing. With JIT, supply chains streamline operations, reduce storage costs, and minimize the risk of parts becoming obsolete before use. However, the success of JIT hinges on seamless coordination and robust supplier relationships.
Safety Stock: Preparing for Turbulence
No flight is entirely immune to turbulence, and the same holds true for supply chains. Safety stock acts as a buffer, providing a cushion against unexpected spikes in demand, supply chain disruptions, or delays. While the goal is to keep safety stock to a minimum to control costs, having a carefully calculated reserve ensures operations stay smooth even when faced with unexpected challenges.
Inventory Tracking Technology: The Eyes in the Sky
Imagine having an eagle-eyed assistant overseeing your inventory around the clock. Inventory tracking technology, such as RFID tags and IoT devices, offer real-time visibility into the location and status of spare parts. This level of transparency allows supply chain managers to make informed decisions, prevent losses, and optimize routes for parts delivery.
Collaborative Supplier Relationships: Smooth Takeoff
Strong supplier relationships are the wind beneath the wings of effective inventory management. Collaboration and open communication with suppliers ensure a steady flow of spare parts when needed. By sharing data and insights, both parties can anticipate demand fluctuations, optimize production schedules, and make informed decisions that benefit the entire aviation supply chain ecosystem.
Conclusion
In the intricate world of aviation supply chains, optimizing inventory management is the compass that guides operations toward efficiency and success. From data-driven demand forecasting to JIT inventory strategies and embracing tracking technology, the steps outlined in this blog are the key to striking the perfect balance between availability and cost-effectiveness. As aviation continues to evolve, so too will inventory management practices, ensuring that planes remain ready to take flight and operations soar to new heights.
Vantage Plus Analytics
Empowering businesses with AI-powered analytics and digital transformation solutions for data-driven success.
Services
Data Analytics
AI & Automation
Blockchain Solutions
Industry Analytics